SELECTION OF PRODUCTS ACCORDING TO THE PARAMETERS
Type
Group
Refractoriness value
Porosity degree
Heat treatment method
Molding process
Binding type 1
Binding type 2
Intended purpose
scope of application
Reference document for product properties
Reference documents for product dimensions
PHKUTT
Type: magnesia spinel
Group: periclase-chrome (MgO ≥ 60%, Cr2O3 4-20%)
Refractoriness value: fire resistance (1580 to 1770°С)
Porosity degree: compacted (Ptot 16-20%)
Heat treatment method: heat treated
Molding process: semidry forming
Intended purpose: repair/construction
scope of application: for slag belt lining of steel teeming furnaces
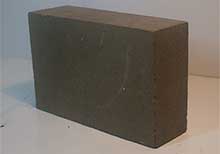
PHSS
Type: magnesia spinel
Group: periclase-chrome (MgO ≥ 60%, Cr2O3 4-20%)
Refractoriness value: high fire resistance (1770 to 2000°С)
Porosity degree: average dense (Ptot 20-30%)
Heat treatment method: burnt
Molding process: semidry forming
Intended purpose: repair/construction
scope of application: for laying of arches of open-hearth furnaces

PHSST
Type: magnesia spinel
Group: periclase-chrome (MgO ≥ 60%, Cr2O3 4-20%)
Refractoriness value: high fire resistance (1770 to 2000°С)
Porosity degree: average dense (Ptot 20-30%)
Heat treatment method: unburnt
Molding process: semidry forming
Intended purpose: repair/construction
scope of application: for melting space arch of open-hearth furnaces, operating without bath oxygen lancing, as well as arches of slag chambers and regenerators
PHSU
Type: magnesia spinel
Group: periclase-chrome (MgO ≥ 60%, Cr2O3 4-20%)
Refractoriness value: high fire resistance (1770 to 2000°С)
Porosity degree: compacted (Ptot 16-20%)
Heat treatment method: burnt
Molding process: semidry forming
Intended purpose: repair/construction
scope of application: for laying of arches of open-hearth and electric-steelmaking furnaces
PHSUT
Type: magnesia spinel
Group: periclase-chrome (MgO ≥ 60%, Cr2O3 4-20%)
Porosity degree: compacted (Ptot 16-20%)
Molding process: semidry forming
Intended purpose: repair/construction
scope of application: for laying of arches of open-hearth, tandem and electric-steelmaking furnaces